Makine Gücü ile Metal Kesme ve Şekillendirme Süreçleri
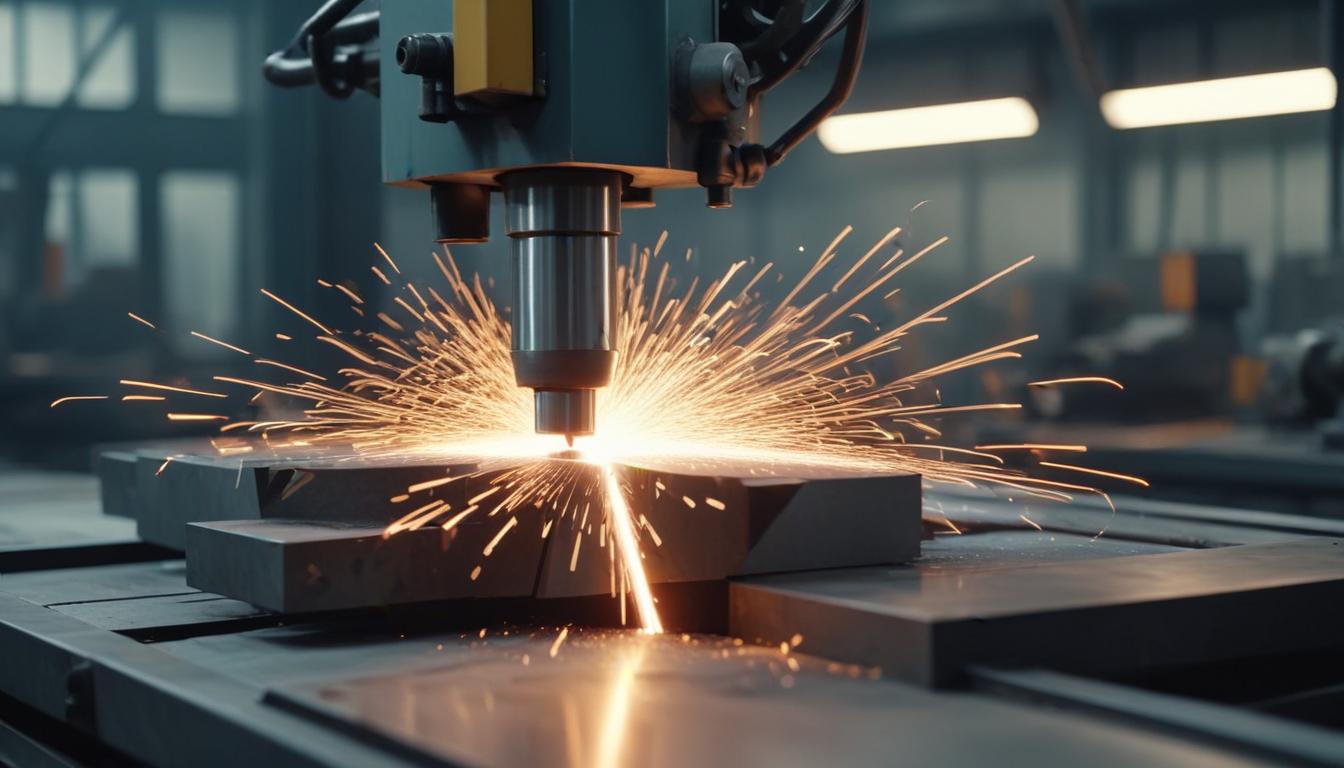
Makine Gücü ile Metal Kesme ve Şekillendirme Süreçleri
Metal işleme, endüstriyel üretimin temel unsurlarından birisidir. Metal parçaların kesilmesi ve şekillendirilmesi, kaliteli ürünler elde etmek için kritik bir süreçtir. Gelişen teknoloji, metal işleme süreçlerini hem hız hem de verimlilik açısından önemli ölçüde geliştirmiştir. Bugün, modern makineler ve kesme teknikleri, üretim süreçlerini daha etkin hale getiriyor. İşletmeler, işleme süreçlerini optimize etme çabasında verimlilik artırma yöntemlerine de yöneliyor. Aynı zamanda, metal işleme endüstrisinde güvenlik ve standartlar da büyük bir önem taşır. İş sağlığı ve güvenliği, makine kullanımı sırasında kritik rol oynar. Makine gücüyle metal kesme ve şekillendirme süreçlerinin tüm yönlerini kapsamlı bir şekilde incelemek, bu alandaki en iyi uygulamaların anlaşılmasına yardımcı olur.
Modern Metal Kesme Teknikleri
Modern metal kesme teknikleri, çeşitli endüstrilerde önemli yer tutan bir konudur. Bu teknikler, yüksek hassasiyet ve düşük hata payı ile çalışmayı mümkün kılar. Kesme işlemlerinde sıklıkla kullanılan tekniklerden bazıları arasında **plazma kesim**, **su jetli kesim** ve **laser kesim** yer alır. Plazma kesim, elektrik arc kullanarak yüksek sıcaklıkta kesim yapar. Bu yöntem, kalın metal eşyaların hızlı bir şekilde işlenmesini sağlar. Bununla birlikte, su jetli kesim işleminde yüksek basınçlı su kullanılır. Bu teknik, ısı hasarını en aza indirerek hassas kesim elde eder. Laser kesim ise, yüksek enerjili lazer ışını ile metal üzerinde kesim gerçekleştirir. Bu yöntem, oldukça ince kesimler oluşturabilen gelişmiş bir tekniktir.
Kesme tekniklerinin seçimi, iş parçasının türüne ve kalınlığına bağlıdır. Maliyet, malzeme ve son ürün gereksinimleri de dikkate alınmalıdır. Örneğin, alüminyum gibi hafif metaller için laser kesim uygundur. Esnekliği sayesinde karmaşık şekiller elde edilebilir. Demir veya paslanmaz çelik gibi daha kalın metaller için plazma kesim tercih edilebilir. Hem ekonomik hem de hızlı bir çözüm sunar. Her tekniğin avantajları ve dezavantajları bulunur, bu yüzden kapsamlı bir analiz yapmak gereklidir. Metal kesim alanındaki gelişmelerle birlikte, sürdürülebilir ve çevre dostu yöntemler de giderek daha fazla önem kazanır.
Şekillendirme Süreçlerinde Kullanılan Makineler
Şekillendirme süreçlerinde kullanılan makineler, metal parçalarının istenilen şekillere dönüştürülmesi için kritik bir rol oynar. Bu makineler arasında **presler**, **bükme makineleri** ve **dövme makineleri** bulunur. Pres makineleri, metalin şekillendirilmesi için genellikle yüksek sıcaklıklara ve basınca dayanıklıdır. Bu makineler, malzemeyi istenen şekle kavuşturmak için dövme, kesme veya bükme işlemlerinde kullanılır. Örnek vermek gerekirse, otomotiv endüstrisinde karmaşık parçaların üretiminde pres makineleri yaygın şekilde tercih edilir.
Bükme makineleri, metalin belirli bir açıya kadar bükülmesini sağlar. Bu makineler, hem ince hem de kalın metal parçaları işleyebilir. Bükme işlemi, inşaat ve metal mobilya üretiminde sıklıkla kullanılır. Dövme makineleri ise, metal parçaların şekillendirilmesinde yüksek sıcaklık kullanır. Bu yöntem, metalin dayanıklılığını artırırken, aynı zamanda istenilen formu elde etmeyi kolaylaştırır. Şekillendirme makinelerinin verimliliği, üretim sürecinin bütünü üzerinde doğrudan etkilidir. İş süresi ve maliyet odağında doğru makinelerin kullanımı oldukça önemlidir.
Verimlilik Artırma Yöntemleri
Verimlilik artırma yöntemleri, metal işleme süreçlerinin optimize edilmesinde önemli bir yere sahiptir. İş süreçlerinin iyileştirilmesi, zaman ve maliyet tasarrufu sağlar. Verimliliği artırmak için **proses optimizasyonu**, **otomasyon** ve **entegrasyon** gibi farklı stratejiler uygulanır. Proses optimizasyonu, kesme ve şekillendirme işlemleri sırasında en iyi sonuçları elde etmeyi hedefler. Örneğin, makinelerin çalışma sürelerinin analiz edilmesi ve bakım süreçlerinin düzenlenmesi, verimliliği artırabilir.
Otomasyon, üretim süreçlerinin hızlandırılmasında önemli bir yere sahiptir. Otomatik makinelerin kullanımı, insan hatalarını minimize ederken, iş gücü maliyetlerini de düşürür. Entegrasyon ise, farklı makineler ve sistemlerin bir arada çalışmasını sağlar. Bu yaklaşım, üretim süreçlerinin daha uyumlu hale gelmesine yardımcı olur. Örneğin, bir üretim hattında kullanılan makinelerin birbiriyle koordineli çalışması, akışı hızlandırır. Verimliliği artırmak, işletmelerin rekabetçilik seviyesini de olumlu etkiler. İyileştirilmiş üretim süreçleri, müşteri memnuniyetini artırma konusunda da kritik öneme sahiptir.
Metal İşleme Güvenliği ve Standartlar
Metal işleme sektöründe güvenlik ve standartlar, yağmalama ve kaza risklerini azaltma adına büyük bir önem taşır. İş yerlerinde meydana gelen kazaların önlenmesi için çeşitli güvenlik önlemleri uygulanmalıdır. İş sağlığı ve güvenliği standartları, çalışanların korunması adına gereklidir. Örneğin, ağır makinelerin kullanımı sırasında uygun koruyucu ekipmanların giyilmesi şarttır. Bunun yanı sıra, iş yerlerinde yangın güvenliği tedbirleri de alınmalıdır. Yangın çıkma riski olan alanlar, düzenli olarak denetlenmelidir.
Standartlar, işleme süreçlerinin belirli bir kalite ve güvenlik seviyesine ulaşmasını sağlar. **ISO 9001** gibi uluslararası kalite standartları, işletmelerin üretim süreçlerini iyileştirmelerine yardımcı olur. Güvenlik eğitimleri, çalışanların olası risklere karşı farkındalığını artırır. Bununla birlikte, enerji verimliliği gibi konular da önem kazanır. Enerji tasarrufu sağlamak hem maliyetleri düşürür hem de çevresel sürdürülebilirliği artırır. Metal işleme sektöründe, güvenlik kültürü oluşturmak ve standartlara uymak kaçınılmazdır.
- Kesme işlemlerinde dikkat edilmesi gerekenler
- Makinelerin periyodik bakımları
- Koruyucu ekipman kullanımı
- Yüksek sıcaklıklara karşı önlemler
- Yangın güvenliği tedbirleri